MRP実行
2.4 MRP実行
② MRP実行
2つ目のプロセスは、MRPの実行です。
このプロセスについては、プロセス自体の説明に入る前に、所要量に関わる2つの大事な概念、「MPS」と「MRP」について理解していきましょう。
MRPとMPSとは
MPS/MRP(所要量計画)は、計画独立所要量、または受注数量を元に、製品や半製品をどのぐらい生産するか、資材をどのぐらい注文すればいいかを計算することです。
MPS・MRPと半製品向け・原材料向けと言葉を使い分けますが、所要量算出の計算ロジックはどちらも同じです。
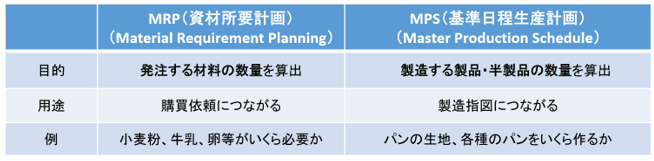
まずMRP(資材所要計画)は、発注する材料の数量を算出するために使われます。
例えば、パンの原料となる小麦粉、牛乳、卵などがあり、この原材料がいくら必要かを決定すると、
購買を管理するMMモジュールへ購買依頼をする作業につながります。
そしてMPS(基準日程生産計画)は、製造する製品・半製品の数量を算出に使用されます。
MPSの対象となるものは、例えば実際製造することになるパン生地みたいな半製品や、完成した製品のパンが考えられます。
このMPSを算出することにより、製造指図を作成することが出来るようになります。
本資料では所要量計算をわかりやすく「MRP実行」を想定して説明していきます。
MRPの算出
MRP実行に関わる要素についてみていきましょう。
MRP実行の段階では、現在の在庫数量、入庫予定数量、出庫予定数量、安全在庫数量をもとに
これから生産する数量・発注する数量を算出します。
- 入庫予定数量:すでに発注が済んでいるが、まだ仕入先から材料が届いてなく、届く予定の数量です。
- 出庫予定数量:生産計画をすでに立てていて、これから材料・半製品を使う予定の数量です。
- 安全在庫数量:万が一に備えて、最低限確保しておくべき在庫の数量です。
これらを用いて、所要量は「計画独立所要量(予測で必要な数量)or 受注数量」と 「現在庫数量・入庫予定数量・出庫予定数量・安全在庫数量」を比較して、必要な生産・購買数量を算出します。
MRP算出の例
MRP算出のロジックをイメージで表現すると、図のような形になります。

今から製造する必要がある不足分、つまり所要量は、この計算式を用いて算出します。

図に書いてある通に、それぞれの項目ごとに任意の数量を上記のように設定すると、今回の所要量は
「4 + 1 + 4 – 3 – 4 = 2」で、「2」であることが分かります。
このように、所要量をもとにいくつ生産するか、または購買するかを計算します。
MRPロジックの概要
ではMRPのロジックがどのように動くかについても見ていきましょう。
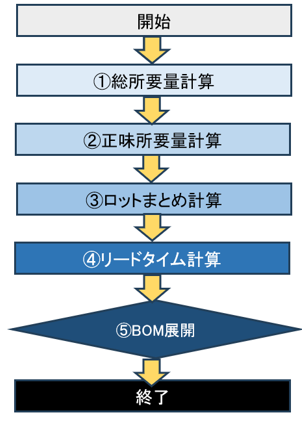
①総所要量計算
MRPの機能で最初に行なわれる計算。
品目の要求数量(所要量)を期間ごとにまとめたものです。
②正味所要量計算
算出された総所要量をもとに、
在庫や注残を加味して算出された所要量です。
③ロットまとめ計算
算出された正味所要量をもとに
ロットサイズに合わせて数量をまとめる段階。
正味所要量を予め部品別に設定してある発注方針に従ってロットにまとめるものです。
④リードタイム計算
納期からリードタイム(作業時間)を差し引き、発注日や作業着手日を算出します。
⑤BOM展開
MRPでは、製品1つを対象とするのではなく、
その製品を構成している部品を含めて計算の対象とします。
例えば、以下のような流れが考えられます。
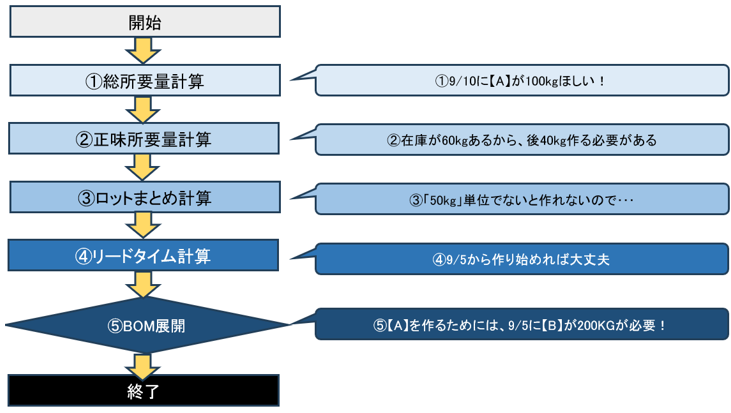
①最初開始の上で、総所要量計算が行われます。
これはMRPの機能で最初に行なわれる計算で、品目の要求数量(所要量)を期間ごとにまとめたものです。「9/10までにAという品目が100kg必要」などの必要とする数量とその納期を決めることになります。
②次は正味所要量計算です。
これは算出された総所要量をもとに、在庫や注残を加味して算出された所要量のことです。
現在の在庫数量が60kgあることを把握し、後40kgが必要という不足分を認識します。
③次はロットまとめ計算です。
ロット(lot)とは、同じ製品をまとめて管理する際の最小単位のことです。
ロットまとめ計算とは、算出された正味所要量をもとに、ロットサイズに合わせて数量をまとめることです。
つまり、正味所要量を予め部品別に設定してある発注方針に従ってロットにまとめるものです。
例えば、この会社のロット単が50kgだと、120kgの製品が必要な際には単位を考慮して150kgを作る、という計算が必要です。
④次はリードタイム計算です。
リードタイム(Lead time)とは、工程や作業の始めから終わりまでにかかる所要時間(期間)です。
納期からリードタイム(作業時間)を差し引き、発注日や作業着手日を算出します。
⑤最後にBOM展開があります。BOMとは「Bill Of Materials」を略した言葉で、
製造業においては、製品に必要な部品を一覧に表した「部品表」を意味します。
MRPでは、製品1つを対象とするのではなく、その製品を構成している部品を含めて計算の対象にします。
例えば、【A】の完成品を作るためには、9/5に部品、つまり半製品の【B】が200KG必要という形です。
MRPの多段階計画
MRP(資材所要量計画)は、多段階での所要量展開により実行することも可能です。
所要量展開とは、MRPの1機能で、作成されたオーダーを基にBOM(部品構成表)を参照して子品目に展開し、各々の品目の所要量の算出を行うことです。
所要量展開の機能は、大きく「一段階展開機能」と「抽出機能」に分けられます。
- 一段階展開機能:部品展開をしながら子品目の所要量を計算し、その結果をローレベルコードの順に登録する。
- 抽出機能:ローレベルコードの上から順に登録されている品目を抜き出す。
さまざまな計画タイプ、ロットサイズ、調達タイプ、不良率等を設定する事で
より適切なタイミングでの適切な調達提案が可能になります。
MRPは製品の生産計画に応じて、MPSの独立所要量に基づき、
生産に必要な資材を算出し、半製品の計画注文を生成します。
生産に必要な自在や半製品の数量を算出するために、BOM(部品構成表)と在庫情報を参照します。
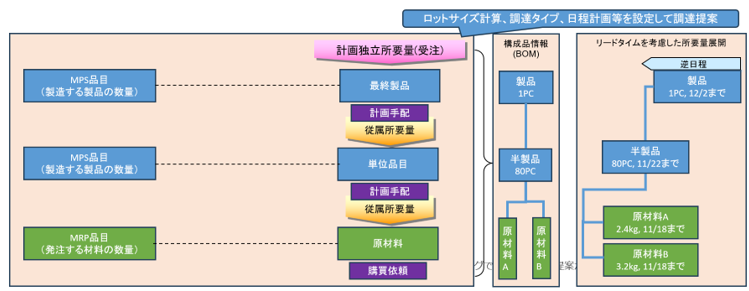
イメージのような、多段階製品構造で、1つの製品に対する計画注文は、従属需要の半製品を生産するために再びMRPに戻り、半製品を生産するに必要な資材を算出する形で進められます。
所要量の計画は、最終製品だけではなく最終製品を制作するための段位品目・原材料に対しても行われ、多段階で構成されます。
例えば、1つの製品を制作するために80個の半製品が必要で、またその半製品を制作するために原材料A、原材料Bが必要になったケースを想定しましょう。
すると、最終製品のリードタイムを考慮して各日程が立てられます。リードタイムとは、生産の現場にて、実際の工程・作業に着手してから、すべての工程・作業が完了するまでにかかる所要時間を言います。
所要量計画はこのように、多段階で行われることを理解しておきましょう。